Introduction
The stock quantity tracking feature of the inventory module helps businesses to keep track of their inventory in real-time, with accurate record of quantities, location and attributes, this feature helps businesses to make informed decisions.
It allows for the tracking of inventory availability in 3 different states, incoming, available and reserved, and updates stock movement automatically through other modules such as sales delivery, purchase receives and batch orders. Additionally, it also allows for manual adjustments to ensure accurate record keeping. Enables businesses to efficiently control and manage their inventory which leads to cost reduction.
Features
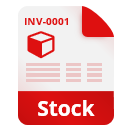
Stock Management
Maintains a master record of all inventory items including dimensions, size, weight, price, and additional information.
Users can view associated selling products and purchase history, and convert units of measurement as needed. Low stock level alerts trigger notifications to respective departments to take further action.
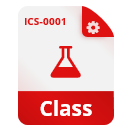
Stock Class
The inventory classification feature allows for classification of inventory items for logistics and warehousing purposes, such as normal, gas, frozen, fragile, heavy, hazard, etc.
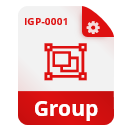
Stock Grouping
The inventory grouping feature allows for differentiation of inventory items based on purpose or quality value, such as normal, return stock, defective stock, pending certifications, refurbished stock, rentals, etc.
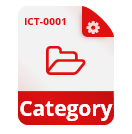
Stock Category
The inventory category feature allows for inventory to be aggregated and reported by similar types for reporting purposes.
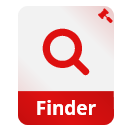
Stock Finder
Powerful tool for searching and locating the whereabouts and availability of inventory items. It displays the breakdown of each stock group, location, variation, and shows source documents that have reserved the stock.
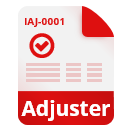
Stock Adjustment
The Stock Adjustment functionality enables adjustments to be made to the inventory count and helps to ensure the accuracy of the stock levels.
It also provides a manual way to perform actions such as adding to or subtracting from the stock without having to rely on the use of the procurement or sales modules.
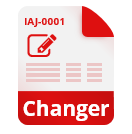
Stock Change
The stock change feature allows for the changes of stock location or the changes of groupings, improves the organization and management of inventory for different purposes.
Highlights
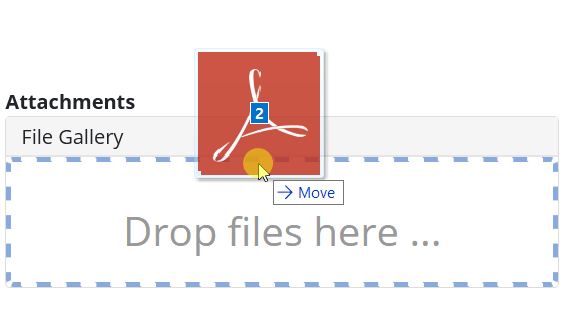
Comprehensive Inventory Tracking
The inventory module allows you to effectively track your inventory in four states: Incoming, Available, Reserved, and Physical. This enables you to stay on top of your inventory levels and make informed decisions about restocking and inventory management during operations.
With the incoming state feature, you can keep a close eye on stock that is on the way, and plan future operations accordingly. This helps you allocate stock before it arrives, reducing overhead costs and increasing efficiency.
The Available state feature provides visibility into the stock that is currently available for use, which can be extremely useful for various purposes. This includes making projections for marketing and promotional pricing strategies, as well as for tracking inventory levels and managing stock replenishment
Reserved state allows you to see the stock that has been set aside for specific orders or projects, which can be useful for ensuring that the stock is allocated correctly and prevent over-allocation.
The Physical state is critical for ensuring the accuracy of inventory levels. By performing regular physical counts, discrepancies between the recorded stock levels and the actual stock on hand can be identified and quickly rectified.
By having real-time physical counts, the inventory audit process can be done regularly, enabling discrepancies to be identified and rectified at any time. This allows for continuous monitoring of stock accuracy throughout the year, as opposed to only during scheduled stock takes.
Having all four states helps to give a clearer picture of the inventory situation and improve the operations of the business.
Processes
Stock In & Stock Out
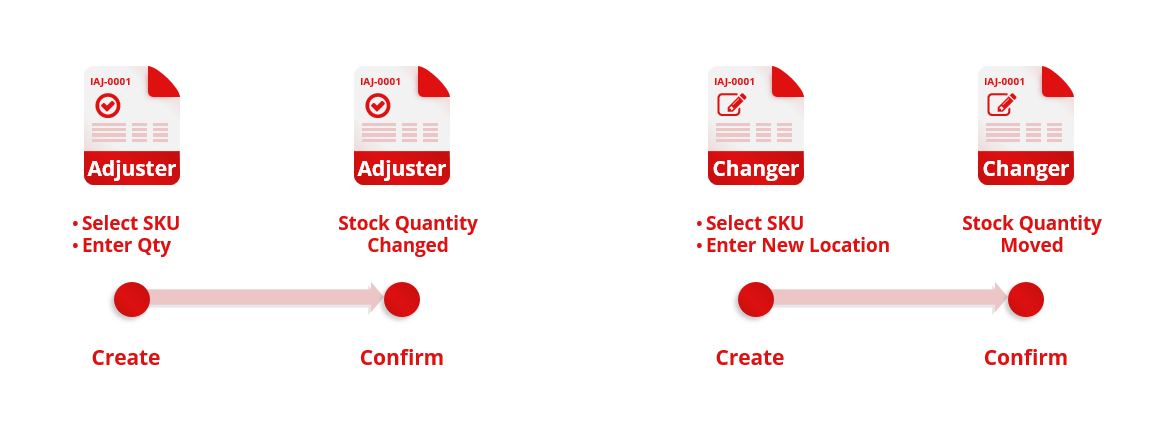
The process of performing a stock adjustment in order to add stock quantities (stock in) or remove stock quantities (stock out) is a straightforward process that can be easily completed within the inventory module.
To begin, a stock adjustment document must be created and the appropriate details such as the description, stock location, and stock group must be entered. Then, select the relevant stock item and populate it with the desired quantities to be added or removed. Once the document is confirmed, the stock’s available and physical quantities will be updated accordingly.
Stock Order Allocation Process
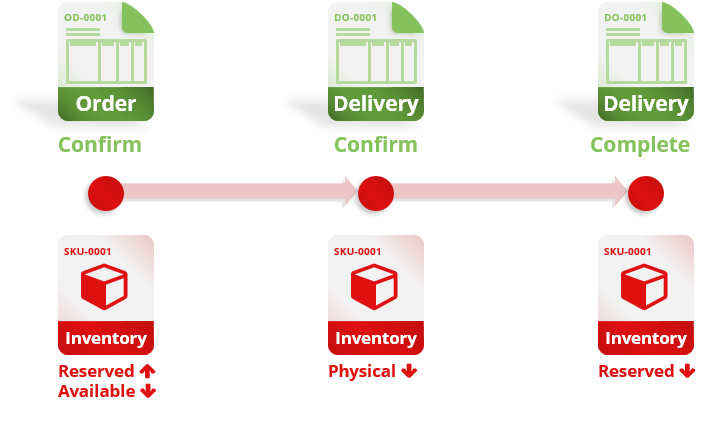
When processing a sales order with stock, for each of the deliverables, enter the required quantity to be allocated for the sales order. This will decrease the available stock and reserve it exclusively for that specific order.
After the sales order is confirmed, the process continues with creating a delivery order. Upon confirmation of the delivery order, the stock that was previously reserved for the sales order will now be reserved for the delivery order.
Once the goods are delivered and the delivery order is mark as completed, the stock will be removed from the system accordingly.
Receiving Purchases
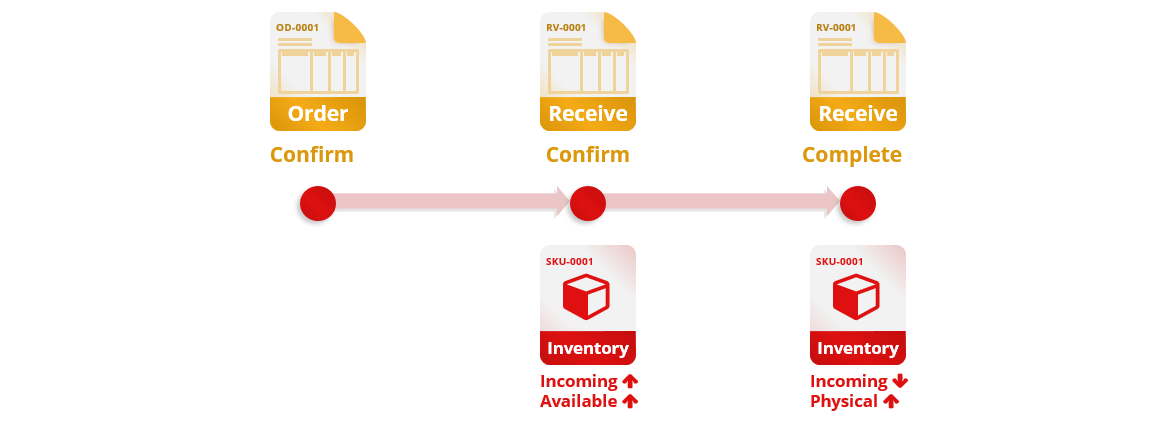
The Purchase Receive process starts with creating a Purchase Order. Then, a Purchase Receive document is created to track the expected delivery. This increases the Incoming count in the inventory.
When the actual delivery happens, the received items are counted and the Purchase Receive document is marked as complete. This moves the items from “Incoming” to Available and Physical count in the inventory.
If some of the items were already reserved for a sales order, they will be moved directly from Incoming to Reserved. This way the reservations made earlier are honored, and delivery orders can be confirmed.
Learn more
Tours
- Bookkeeping & Automation
- Tips to do thing and that
Tutorials
- Bookkeeping & Automation
- Tips to do thing and that